Walid HARIZI Enseignant-chercheur
Maître de conférences | IM - Ingénierie Mécanique | ROBERVAL - Mécanique, Energie et Electricité
In order to overcome these constraints, and drawing inspiration from the human nervous system which is a set of interconnected entities transmitting information to the different organs, the solution is to integrate, from the manufacturing stage, piezoelectric transducers inside the material and thus develop smart searchable composite structures (Figure 1).
The main objective of my research works is to instrument PMC structures with a network of piezoelectric sensors (Lead Zirconate Titanate LZT or PZT and/or PolyVinylidene Fluoride PVDF) to monitor their health state in real-time during their lifespan. These sensors can be used in passive (as acoustic emission sensors or planar capacitors) or active modes (Lamb wave generators). The scientific and technological challenges to develop the SHM of composite structures are very numerous.
These include:
- The integration of sensors in a fibrous environment: what about intrusiveness?
- Relationship between the physical phenomena due to damage and the response of the PZT sensors integrated within the material?
- In the case of a complex PMC structure, the positioning choice of the sensors related to the damage to be detected?
The design of health monitoring systems for composite structures, based on embedded piezoelectric sensors, requires the use of numerical tools able to deal with the complex mechanics of layered materials, as well as, multifield problems. Classical Finite Element Models have been proved to be inaccurate in the analysis of layered structures and extremely computationally expensive when high accuracy, obtained using three-dimensional elements, is required. A new generation of numerical models is thus required to predict/detect the failure of composite materials.
Recent publications:
- Harizi, W., Azzouz, R., Martins, A.T., Hamdi, K., Aboura, Z., Khellil, K. “Electrical resistance variation during tensile and self-heating tests conducted on thermoplastic polymer-matrix composites”. Composite Structures, Volume 224, 15 September 2019, 111001.
- C. Tuloup, W. Harizi, Z. Aboura, Y.Meyer, B. Ade, K. Khellil. “Detection of the key steps during Liquid Resin Infusion manufacturing of a polymer-matrix composite using an in-situ piezoelectric sensor”. March 2020. Materials Today. DOI:10.1016/j.mtcomm.2020.101077.
- C. Tuloup, W. Harizi, Z. Aboura, Y. Meyer, K. Khellil, R. Lachat. “On the use of in-situ
- C. Tuloup, W. Harizi, Z. Aboura, Y. Meyer, K. Khellil, R. Lachat. “On the use of in-situ
piezoelectric sensors for the manufacturing and structural health monitoring of polymer-matrix composites: A literature review”. Composite Structures vol. 215, pp. 127–149, 2019.
- C. Tuloup, W. Harizi, Z. Aboura, Y. Meyer, K. Khellil and R. Lachat. “On the manufacturing, integration, and wiring techniques of in situ piezoelectric devices for the manufacturing and structural health monitoring of polymer–matrix composites: A literature review”. Journal of Intelligent Material Systems and Structures 30(16), pp. 2351-2381, 2019.
- C.Tuloup, W. Harizi, Z. Aboura and Y. Meyer. “Real-time monitoring of the infusion process of a polymer-matrix composite with an embedded piezoelectric transducer”. SMART 2019:IX ECCOMAS Thematic Conference on Smart Structures and Materials. Paris, France. July 2019.
- C.Tuloup, W. Harizi, Z. Aboura and Y. Meyer. “Real-time monitoring of the infusion process of a polymer-matrix composite with an embedded piezoelectric transducer”. SMART 2019:IX ECCOMAS Thematic Conference on Smart Structures and Materials. Paris, France. July 2019.
- C. Tuloup, W. Harizi, Z. Aboura and Y. Meyer. “Structural health monitoring of smart polymer-matrix composite during cyclic loading using an in-situ piezoelectric sensor”. ICCM22: 22nd International Conference on Composite Materials (ICCM22). Melbourne, Australia. August 2019.
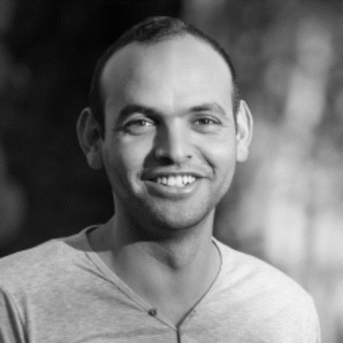
Contacts
Walid HARIZIMaître de conférences
Roberval - UTC
Centre de Recherche
Rue Roger Couttolenc,
60200 Compiègne
E-mail : walid.harizi@utc.fr
Tél. : +33 (0)3 44 23 46 23